BRAKE Caliper Replacement: How to Replace Brake Caliper
If you’re considering a brake caliper replacement, the following guide will help guide you through the process one step at a time.
A caliper will normally leak between the piston and seal, causing the piston to seize-up, ultimately locking-up the brakes up. Rust and corrosion near the housing seal of the caliper piston are responsible for causing this issue. The brake fluid’s exposure to moisture and dirt leads to detrimental effects on the rubber seal of the caliper piston, resulting in damage.
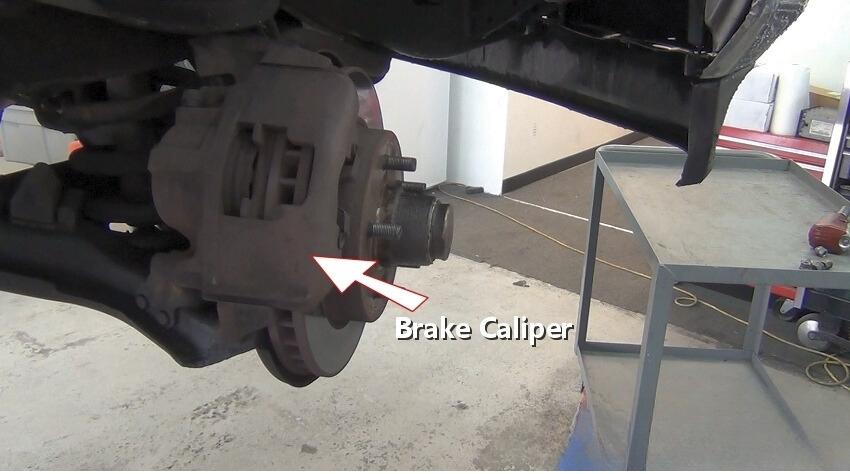
Symptoms of a Bad Brake Caliper
- Fluid leak
- Overheating brakes
- Car pulls either to the right or left when applying the brakes
- Uneven brake pad wear
- Brakes not releasing
Future note: When the piston is pushed back into the caliper housing to accommodate new brake pads, there’s a risk of inadvertently compromising the seal, which can cause a potential leak. So be careful not cause damage by pushing too fast.
Tools and Supplies Needed
- Rebuilt Brake caliper
- Tool set
- Line wrench set
- Brake fluid
- Needle nose vise grips (optional)
- 1/4 Fuel line (optional)
- Brake caliper lube
- Brake cleaner
- Vacuum cap assortment
Step 1
Remove the Brake Caliper Mounting Bolts: To identify the caliper requiring replacement, it is essential to replace only one caliper at a time. This approach helps manage brake fluid leakage and minimizes confusion during the job. Begin by using a wrench or socket to remove the caliper slide bolts. Since these bolts can be tightly secured, ensure that the tool is squarely positioned on the bolt’s head before exerting pressure to loosen it. Next, firmly grasp the caliper and vigorously rock it back and forth. This motion creates a small air gap between the caliper piston and brake pads.

Step 2
Removing the Brake Line: After removing the caliper mounting bolts, there are two approaches to prevent brake fluid from leaking out of the master cylinder when the brake line is disconnected. The recommended method involves detaching the brake flex hose from the frame brake line and utilizing a rubber cap to plug it off. This approach is preferred because, when the caliper line is removed, the master cylinder can drain out its fluid, resulting in difficulties when bleeding the system. Moreover, this presents an opportune moment to consider replacing the brake line.
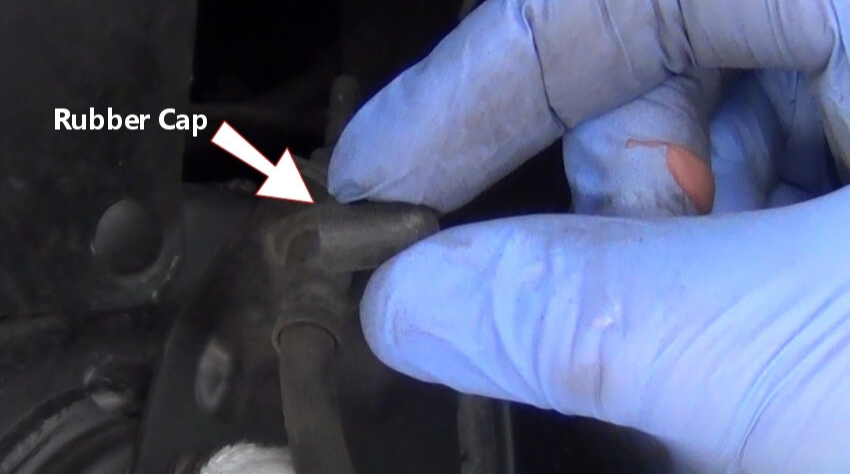
When locating the brake line’s connection to the frame mount, ensure a precise identification of the attachment point. Then, employ a line wrench to loosen the fitting. It is important to use a line wrench rather than a regular wrench due to the tightness of these fittings. Using a regular wrench can potentially round the fitting, causing complications when attempting to remove it.
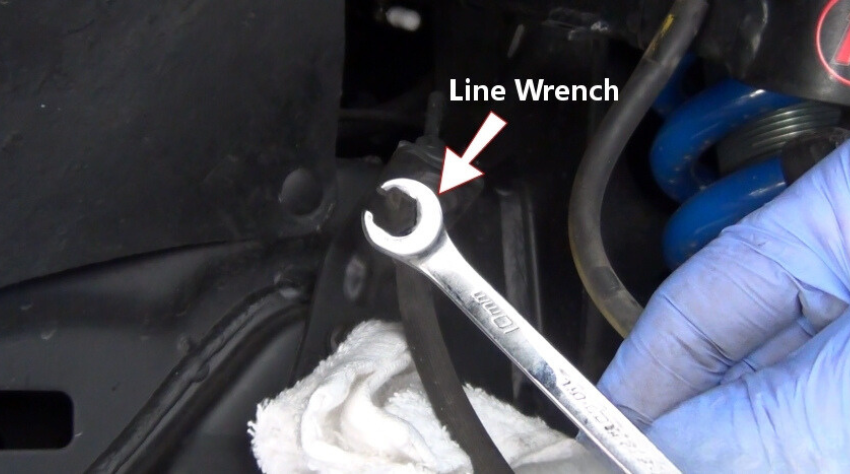
Once you have the line broken free, you can use a regular wrench to speed things up, to remove the fitting. Brake fluid will begin to leak out slowly.
After the line is loose brake fluid will be dripping from it metal tube so be ready with a shop towel to catch it.
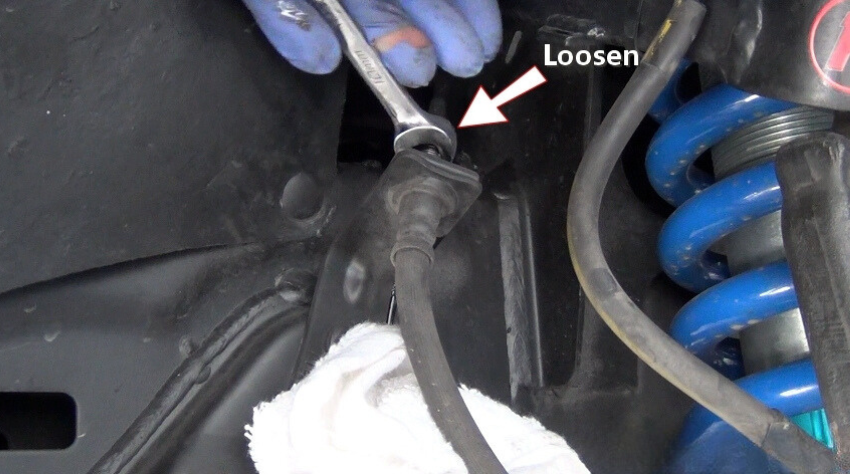
Next, take the rubber cap and securely fit it over the metal brake line to create a reliable seal and prevent fluid leakage. Afterwards, use a shop towel to meticulously clean up any excess fluid. For a thorough cleaning, flush the area with a combination of water and soap, ensuring a pristine finish.

Here’s the other approach to prevent brake fluid from leaking. Take two pieces of fuel line and cover the jaws of a pair of needle nose vise grips.
Adjust the vise grip tool to delicately pinch the rubber brake hose, aiming to halt the fluid flow without causing harm. It is crucial to exercise caution and avoid applying excessive force to the vise grip, as this can lead to damage. If the brake line exhibits cracks or leaks, it is advisable to replace both the line and the caliper. However, it’s worth mentioning that certain mechanics opt against this method due to concerns that overly tightening the vise grip may degrade the internal lining of the hose.

Now, proceed to remove the brake line from the caliper. To aid in reassembling it correctly, make a mental note or use your cell phone to capture a picture of the brake line’s configuration from the frame to the caliper. This visual reference will serve as a helpful guide. Locate the mounting bolt, sometimes called a banjo fitting, and use a socket or wrench to loosen it. Be prepared for a small amount of brake fluid to leak out during this process, as it is a normal and expected outcome.
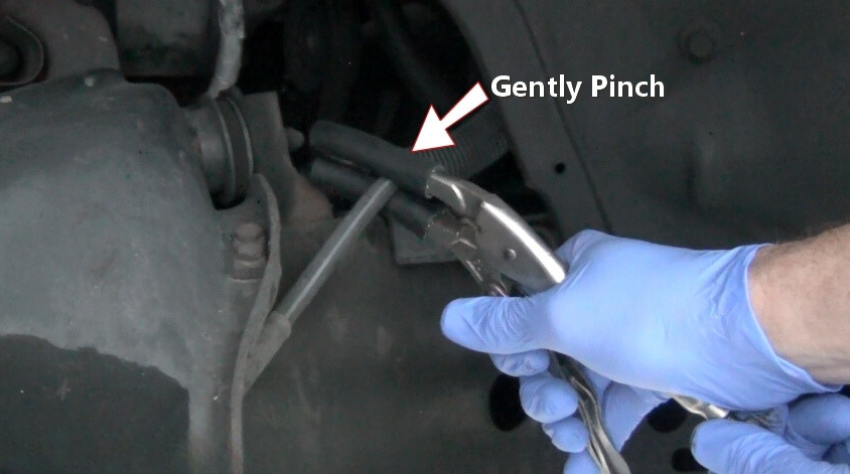
During the process, you will come across two sealing washers located on either side of the brake line bulkhead fitting. These washers, commonly made of copper or aluminum, must be replaced, and they are usually included with the replacement calipers. If you find it challenging to loosen the fitting, reattach the caliper onto the mounting bracket to secure it in place while undoing the banjo bolt. Once the line has been successfully undone, ensure a firm grasp on the caliper to prevent any injuries, as its weight can pose a hazard if it accidentally falls.
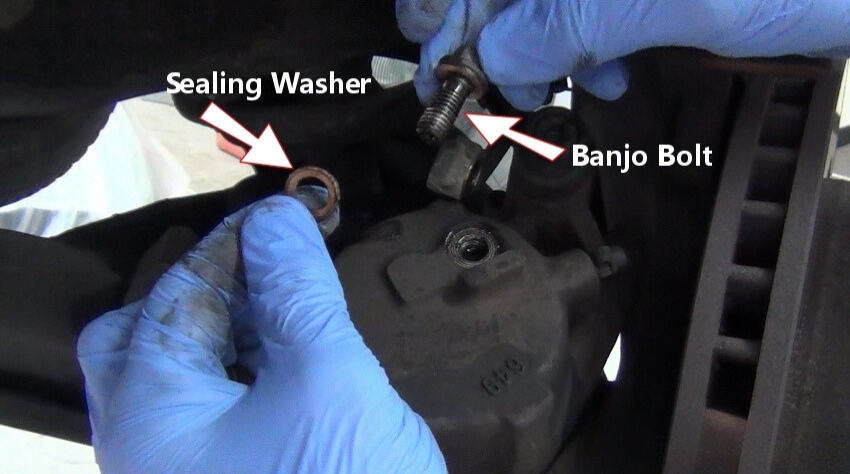
Step 3
Caliper Removal: Hold onto the caliper firmly and carefully disconnect it from both the mounting bracket and the rubber flex hose. It is normal for a small amount of fluid to leak out during this step. At this point, we are ready to move forward and compare the old caliper to the new unit for a proper match.
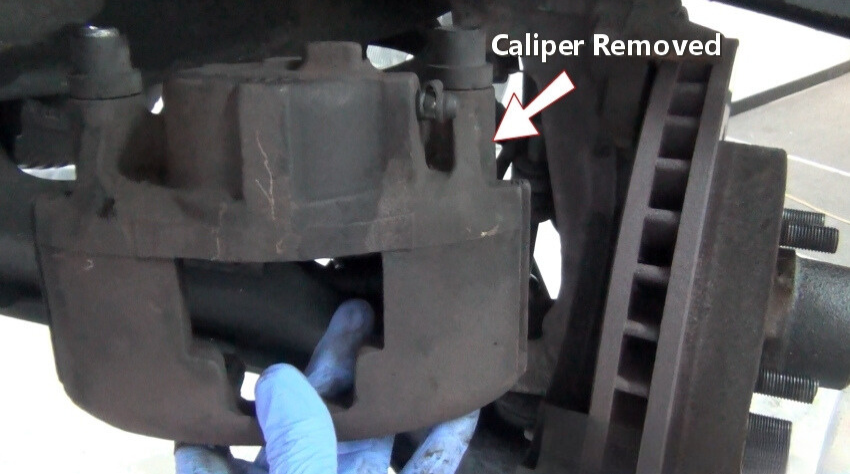
Step 4
Clean the Brake Line Mount: Securely hold the brake line and use a shop towel to meticulously clean the end, ensuring the removal of any dirt and corrosion. It is important to thoroughly clean both the top and bottom surfaces, as the presence of any obstacles can lead to leaks in the sealing washers.
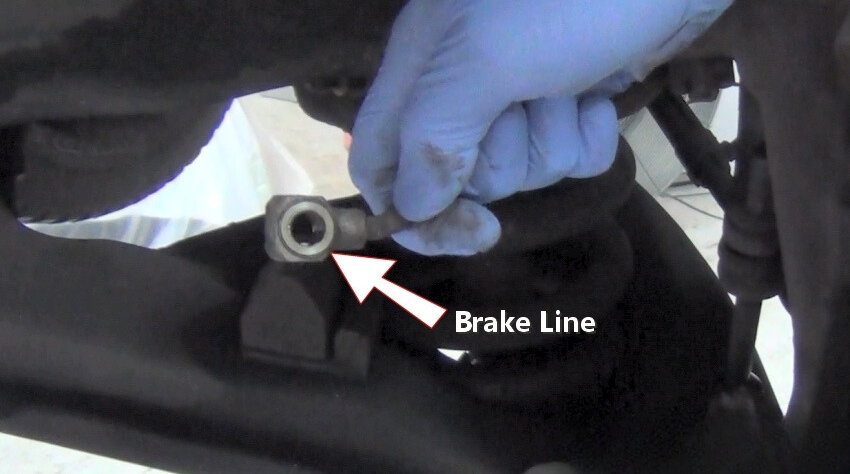
Step 5
Prepare the New Caliper for Installation: Maximize the chances of a successful brake job by acquiring a reliable rebuilt brake caliper set. Don’t let the frustration of leaks or poor performance due to subpar rebuilds dampen your efforts. Choose a reputable name brand from reputable sources like Amazon or a local auto parts store. Keep in mind that certain rebuilt calipers may come with a core charge, so hang onto the old calipers as they hold some monetary value. Return the calipers in their original packaging, and to contain any potential brake fluid leaks, it’s advisable to store them in a plastic bag during transportation.
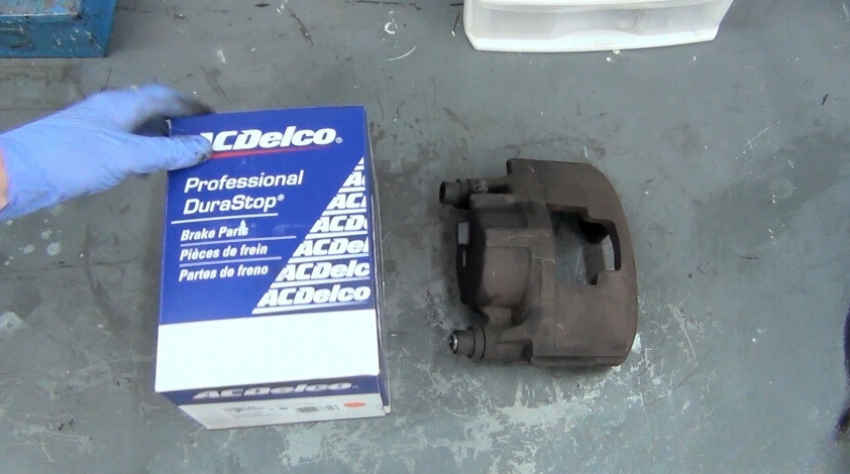
When ordering new calipers, some models may come bundled with new pads and hardware, such as sliders, which play a crucial role in maintaining proper caliper operation. It is vital for the caliper to have the necessary movement freedom while securely attached to its mounting bracket. This unrestricted movement allows for even pad wear and ensures optimal braking performance for the vehicle.
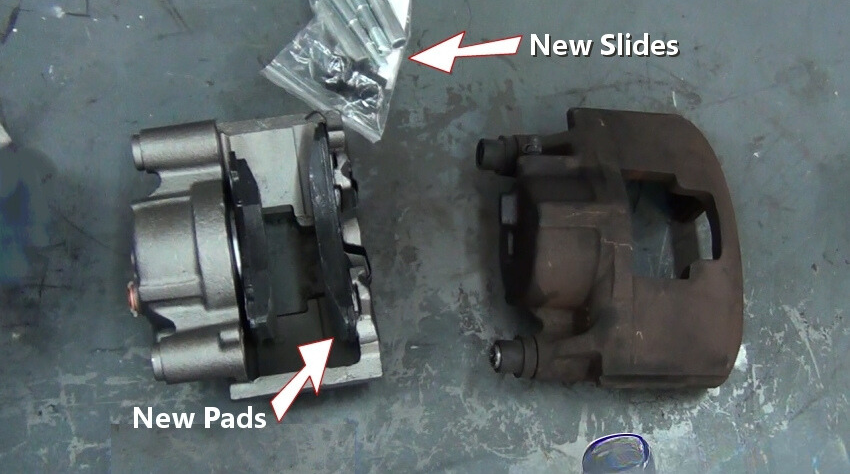
As you inspect the brake fluid port, you will notice the presence of a dust cap, which may house the new sealing washers included with superior rebuilt calipers. To remove the cap and access the port, employ a flat-blade (standard) screwdriver. After removing the cap, set the washers aside for future installation.
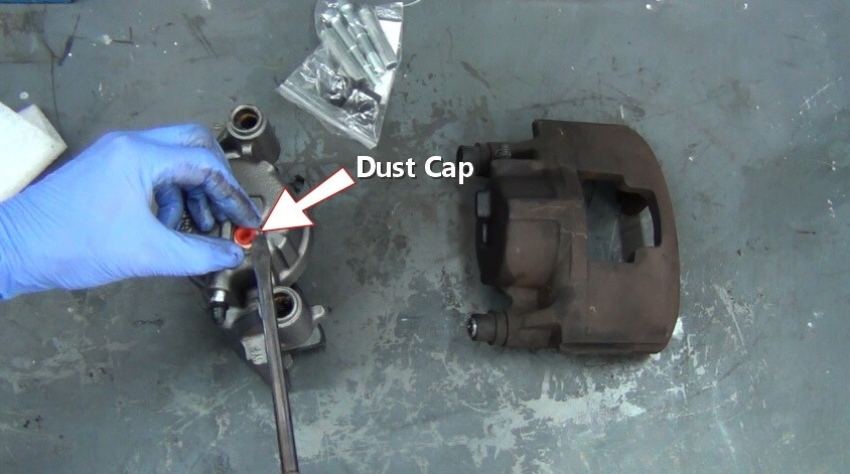
Carefully unpack the plastic bag accompanying the caliper and retrieve the slides enclosed within (unless they have been pre-installed by the rebuilder). Depending on the specific caliper, the slides may come pre-lubricated or necessitate the application of a small quantity of brake lube. Ensure that the slides are adequately lubricated during installation, as neglecting this step can lead to caliper sticking, resulting in uneven brake pad wear and potential brake pull.

Keep in mind that some calipers feature a dust boot designed to shield the slides from moisture that could interfere with the caliper’s optimal functioning. To install the dust boot, employ a hammer and socket, gently applying pressure to position the rubber seal correctly. It may require some perseverance, so it is advisable to meticulously inspect and confirm that the seal is completely seated in place.
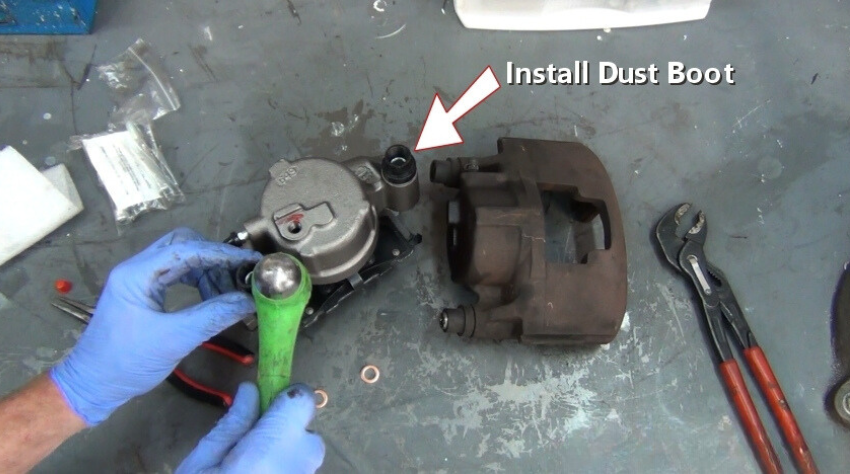
With the caliper prepared for installation, begin by pushing the brake pads into the piston and outer plate. This step facilitates the smooth installation of the caliper over the rotor and caliper mounting bracket. Occasionally, during shipping, the piston may be pushed slightly outward. If this occurs, it can be easily re-inserted by using your hand or employing a large C clamp or channel locks.
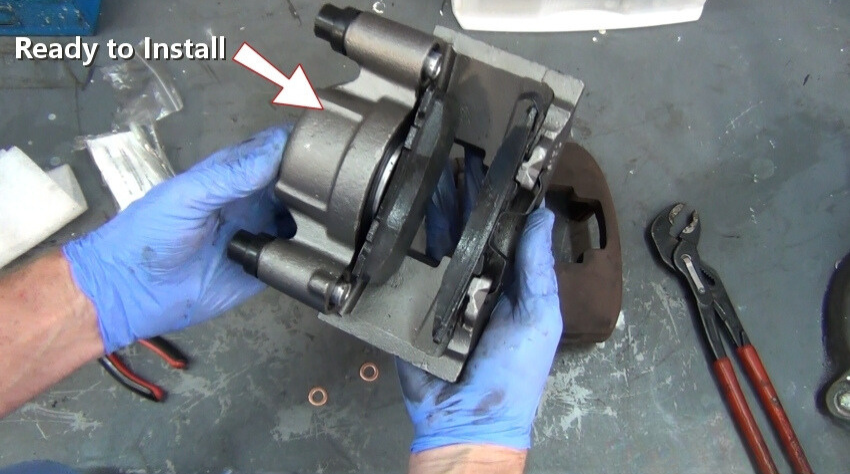
Step 6
Install New Sealing Washers: Prior to installation, ensure the banjo bolt is meticulously cleaned using a shop towel and brake cleaner. Take the time to inspect the bolt for any cracks or scores on the sealing surface. If any damage is detected, it is essential to replace the bolt promptly to prevent potential leaks and maintain optimal performance.

Most rebuilt calipers come with new mounting hardware, including bolts and additional sealing washers, which are essential for completing the installation process with a professional touch. By utilizing the provided mounting hardware, you ensure a secure and reliable attachment. Additionally, when reinstalling the hose, it is advisable to replace the existing copper sealing washer with a new one for optimal sealing performance.
STEP 7
New Caliper Installation: While maintaining a firm grip on the caliper, position it closely and proceed with the installation of the clean banjo bolt. Ensure that the inner sealing washer is still intact as you carefully guide the bolt through the brake line fitting. Once the bolt is in place, proceed to install the outer sealing ring. With both seals properly installed, the brake line is now prepared for installation, marking the completion of this stage.
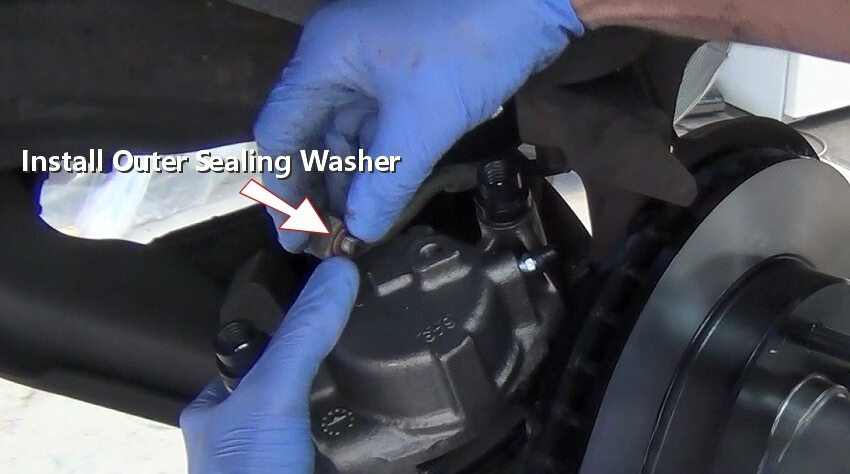
Thread the bolt inward into the caliper by hand to avoid cross threading. Position the brake line in the correct orientation (with out bends or twists). Tighten the bolt firmly to help seat the sealing washers. Don’t over tighten them because the bolt is hollow and it can break.
Keep a close eye on the brake flex hose to ensure it remains untwisted as you position the caliper over the rotor and lower it onto the mounting bracket. Exercise caution to prevent any unintended contact or excessive force on the pads and rotor during installation. Remember, it is important to refrain from using a hammer to install the caliper, as it should fit into place smoothly and effortlessly.
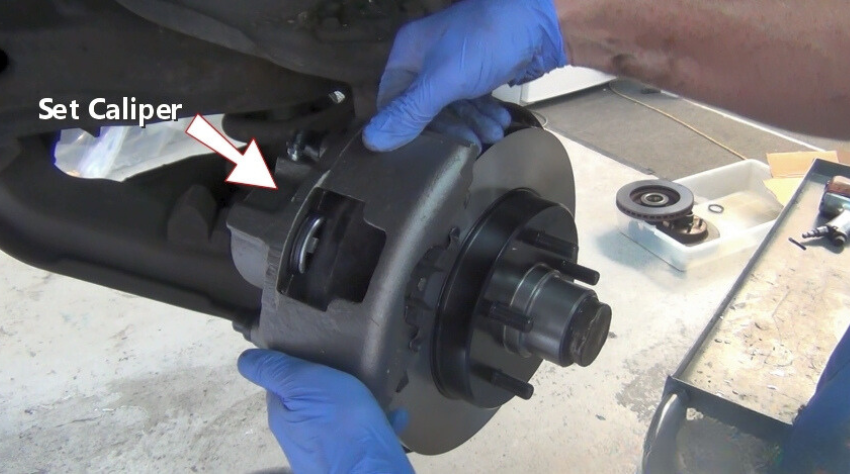
If you have issues getting the caliper all the way down, just pull the caliper back up and check the slides to make sure they’re fully retracted into the housing by repositioning them outward.
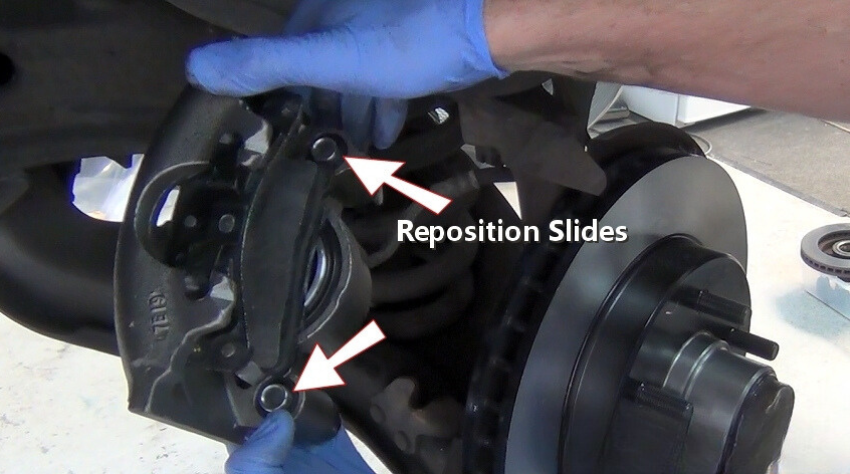
After lowering the caliper over the rotor and onto the mounting bracket, it is time to install the new mounting bolts. Take caution to thread them in by hand to prevent cross-threading, especially if the manufacturer has applied thread lock, such as lock-tight. This step might require some slight adjustments and manipulation to get the bolts started, so remain determined and patient. For added assistance, you can push the rotor onto the bearing hub. Proceed to hand-thread both bolts into the bracket until they are snugly secured.
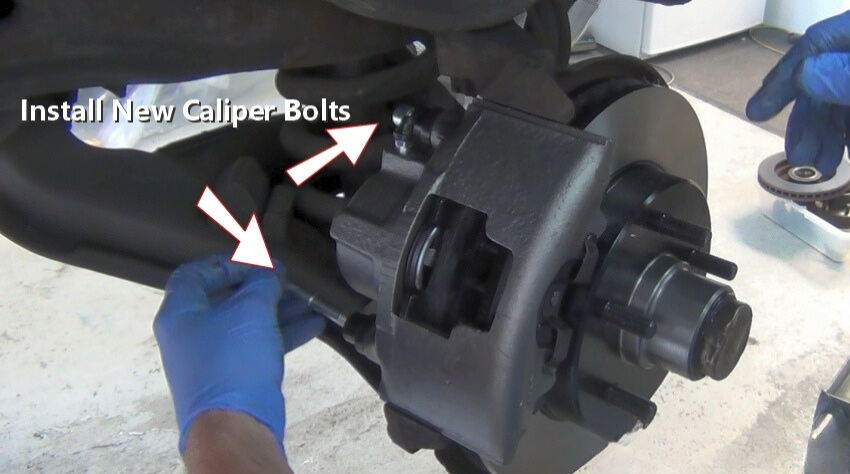
Use a wrench or socket to tighten the mounting bolts evenly while re-checking the tightness with a torque wrench. Most manufactures will tighten these bolts from 40 to 50 foot pounds.

Reinstall the brake line into the fitting and tighten using the boxed end of the wrench.
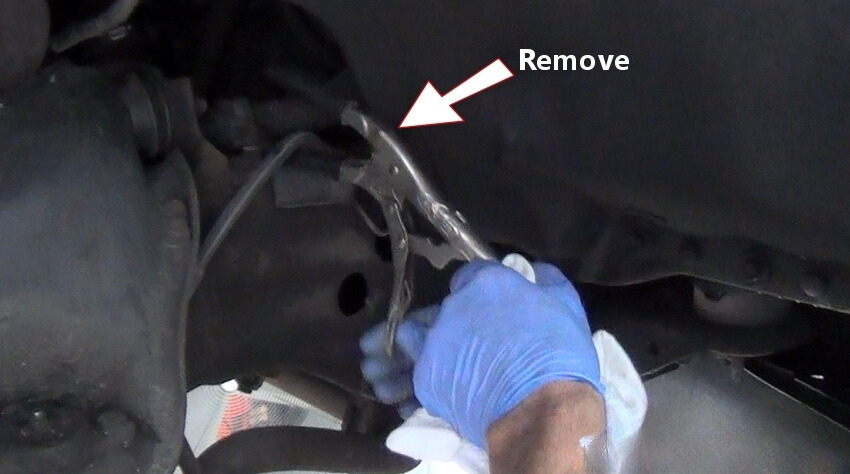
Begin by removing the brake line locks, allowing the brake fluid to enter the caliper. It is normal for the rubber line to display a minor indentation from the clamp; however, this will be rectified as the brakes are applied for the first time. To conclude this repair and maintain the system’s effectiveness, bleeding the brake system is crucial. After successfully bleeding the brakes, carefully assess the brake pedal’s operation. Ensure that the wheel is securely reinstalled before driving the vehicle. Never operate a car with an unreliable brake pedal. During your drive, remain attentive to any unusual noises and promptly reevaluate the repair if needed.
TO SUM IT UP:
It is important to note that brake fluid is corrosive and can harm the vehicle’s paintwork. In the event of fluid contact with a painted surface, promptly use a clean cloth to wipe it off. Follow up by washing the affected area with soap and water to mitigate any potential damage. When conducting brake work, it is crucial to flush and bleed the brake system to prevent the accumulation of moisture, which can lead to rust formation. Remember, any time the brake system is opened, a brake system bleed is necessary.